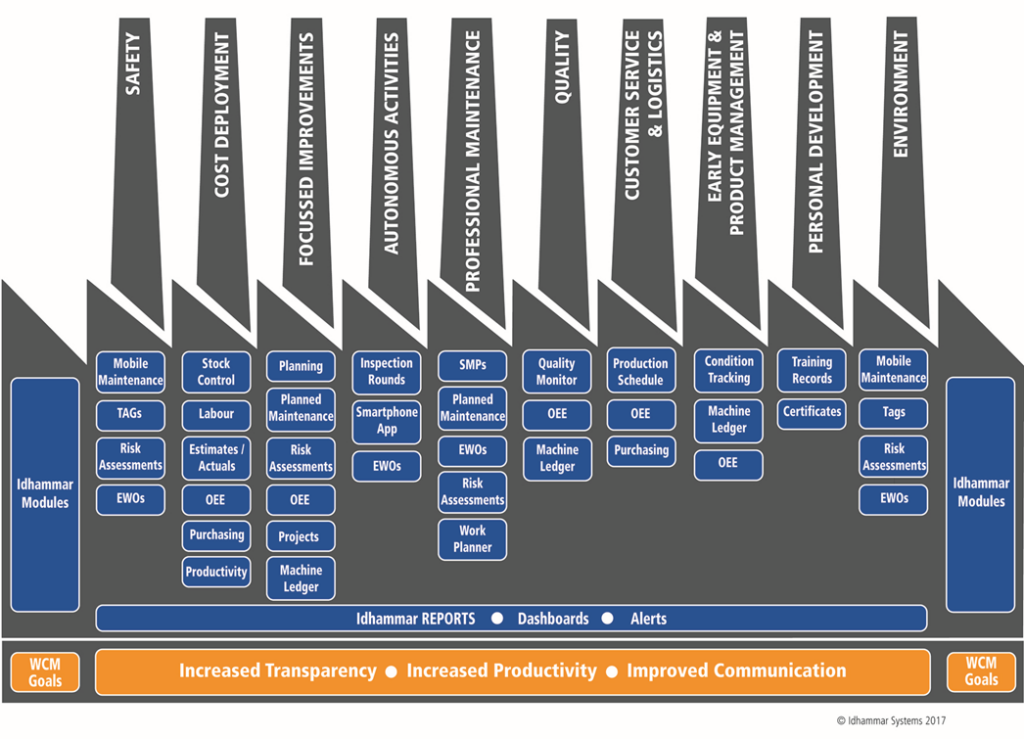
World Class Manufacturing is the philosophy of being the best, fastest, and lowest cost producer of a product. In the past, Computerized Maintenance Management Systems were merely seen as a tool for maintenance managers and engineers to manage work. Nowadays, their potential is far greater; when using these tools in an WCM environment, organisations have the means to transform maintenance operations by working towards the goal of zero defects and zero waste.
Idhammar WCM is designed to lead organisations towards the ultimate cost efficiency. Read on to discover how it supports the 10 pillars of World Class Manufacturing.
The 10 Pillars
1. Safety
Safety should be a priority for all manufacturing plants, the main goal being to reduce the number of accidents and create a culture of prevention.
Our Computerized Maintenance Management Software makes it easier for organisations to be EHS compliant in many ways. For example, the TAG system ensures that operators can quickly record defects so that maintenance can be scheduled before any incidents occur.
In addition, the Core Analysis module helps to detect and eliminate risk through its root cause analysis and ‘what-if’ reports.
2. Cost Deployment
The goal of cost deployment is to precisely determine the causes of loss, whether that’s due to inventory or productivity, among other factors. Idhammar helps you to meet this goal by determining the right costs to cut.
For example, the Overall Equipment Effectiveness module drives cost reduction by capturing and analysing every detail about production performance and assists in identification of where the top losses are occurring; that includes details about assets, shifts, products, or work orders. In addition, rates of labour for various skill levels can be set, giving an accurate score for Overall Labour Effectiveness which provides vital insights into productivity.
3. Focused Improvement
The objective here is to reduce the most critical losses – as well as activities that do not provide value – in order to reduce the most critical losses and to eliminate non value added activities so as to increase the competitiveness of the cost of the product.
Idhammar’s Line Data Portal gathers information from production lines relating to stoppages, performance and quality. The reporting suite allows data to be sliced and diced to aid understanding of the biggest losses and their root cause. What if scenarios can be generated to provide insight into potential cost savings if problems were eliminated. With that said, the reporting capabilities of our wider solution are far more extensive.
The Reporting module gives instant, real-time insights into performance against KPIs and sends automatic alerts when necessary, helping to accelerate response times. This data is also visible on Andon boards placed at the end of each production line. The result is continuous insight into whether targets are being met.
4. Autonomous Maintenance
Autonomous maintenance is a maintenance strategy where operators continually monitor their equipment, make adjustments and perform minor maintenance tasks on their machines. This is done rather than assigning a dedicated maintenance technician to perform maintenance and regularly scheduled upkeep.
Checklists can be prepared for the operator to undertake inspections and line walks and give step by step instructions for fixing simple problems
Of course, developing workers’ competence is another key to autonomous maintenance – we provide training to ensure they get the most out of our software (see point 9 below).
5. Professional Maintenance
The pillar of professional maintenance aims to improve efficiency through failure analysis. The Core Analysis module accelerates your progress towards reaching the ultimate goal of zero breakdowns. In addition, the machine ledger provides comprehensive insights into the condition of all equipment and components; this kind of oversight is crucial in asset tracking, helping workers to predict and prevent failures.
To be most effective Root Cause Analysis should be conducted by cross departmental teams.
6. Quality Control
The Overall Equipment Effectiveness Monitoring module generates data for auditing and quality assurance purposes. Users can set up alerts relating to sub-standard production, enabling them to address issues without delay.
7. Logistics and Customer Service
The inventory management module reduces stock control costs through smarter purchasing, and real-time inventory management means that there’s no need for engineers to waste journeys checking for parts. Waste is therefore reduced thanks to less time being spent waiting for materials. In terms of customer service, the quality control features mentioned above ensure issues are resolved quickly and that you can continue to meet customer requirements.
8. Early Equipment Management
For most effective results it is essential to involve Commercial, Engineers and Operators in the decision-making process. When making a capital spend decision it is important to identify and eliminate hidden losses such as poor maintainability, operability, reliability, safety and environment. Idhammar’s Project module is ideal for co-ordinating cross departmental Tasks required to onboard new equipment.
9. People Development
Our solutions are a catalyst for professional development, helping your maintenance teams exceed their current performance however World Class Manufacturing requires total commitment from all areas of the business. Our knowledge base, standard training and tailor-made courses enable staff to get the best out of the system and as a result, further your organisation’s continuous improvement goals.
Refresher training and advanced courses are also available and we recently launched a knowledge base featuring a great deal of content.
10. Environment
OEE Monitoring provides real-time data on water and energy consumption, not only helping compliance with environmental management standards but saving costs, and embedding an energy-conscious culture within your organisation.
Conclusion
The 10 Pillars of World Class Manufacturing help organisations to perform better and reduce costs and other waste. Our maintenance and OEE software supports each pillar, helping you to achieve these goals and meet all safety, legal and environmental requirements. With professional and autonomous maintenance procedures established, faults will be detected as early as possible, preventing accidents and downtime.
Idhammar Systems are proven to deliver year-on-year reductions in maintenance costs of 5-15%. Contact us to learn more or book a demo.